Sandvik roadheader powers progress in South Korea
- Topics:
- Customer stories
- Published:
- 11 July 2025
- Text
- Jamback Media AB
- Photo
- Jamback Media AB
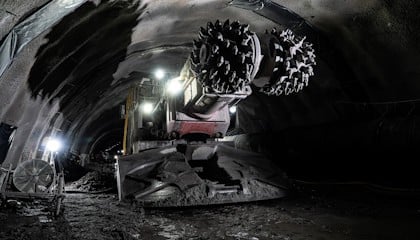
In the buzzing outskirts of Seoul, in the city of Anyang, a transformative infrastructure project is quietly carving its way through bedrock. This is no ordinary excavation effort. It's a bold engineering project led by South Korean construction giant SK Ecoplant, powered by Sandvik's advanced MT720 roadheader and technology. Together, they are changing the way tunneling is done in Korea.
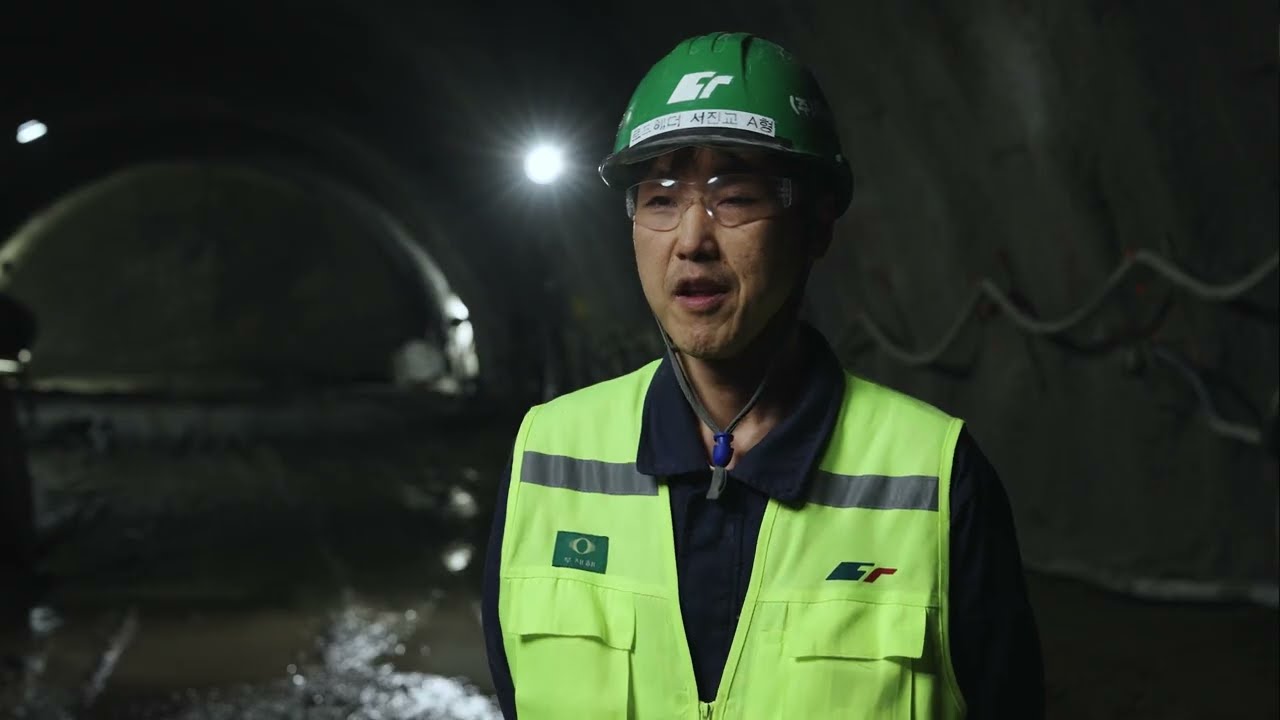
Challenging ground beneath a growing city
The Indeokwon–Dongtan double-track railway project spans over 2.3 kilometers, with one of the most technically demanding sections falling right under a major eight-lane road. Vibration and noise levels had to be strictly minimized to avoid disruption to the urban environment above. To make things even more challenging, the team had to cut through a mix of ground types including hard rock exceeding 100 MPa in strength.
"This project is located in an urban area, and we had to excavate a tunnel under a heavily trafficked road. That made noise and vibration extremely important considerations," Jun-Won Eom, Senior Manager, Geotechnical Engineer at SK Ecoplant.
Indeokwon–Dongtan Railway Project
Location: Anyang, Seoul Metropolitan Area, South Korea
Tunnel length: 2.3 km (1.3 km with roadheader)
Rock strength: >100 MPa
Machine used: Sandvik MT720 (rebuild from Australia)
Progress: 600 meters excavated, 700 meters remaining
Main benefits: Low noise, low vibration, high precision, safety
With teamwork, cutting-edge technology, and shared vision, SK Ecoplant and Sandvik are laying the groundwork for the future of tunneling in Korea one meter at a time.
The Sandvik MT720 used in this project is no ordinary machine. It was previously successfully deployed in Australia, refurbished, fine-tuned and then shipped to Korea for a second mission, a sustainability angle that adds value to an already high-performing solution.
"We are very proud of the machine," said Daniel Forcher, Sales Area Support Manager Tunneling at Sandvik. "It’s not only capable of handling rock strength up to 140 MPa, but it does so using patented electronic control software that no other supplier in the world can offer."
“I attended the training knowing nothing, but after the training, actually operating the equipment helped tremendously.”
Innovation meets reliability - Sandvik MT720 in Action
The Sandvik MT720 has proved to be a game-changer for SK Ecoplant. Operating in such tough conditions requires more than brute force; it requires smart control. That’s where Sandvik's ICUTROC® cutting technology and its advanced automation capabilities come in.
"I was honestly frightened at first," admitted roadheader operator Kim Hong-joo. "But after working with the MT720, I felt a strong sense of pride. Operating this equipment is precise and efficient. It communicates with the optical system and reduces excavation time."
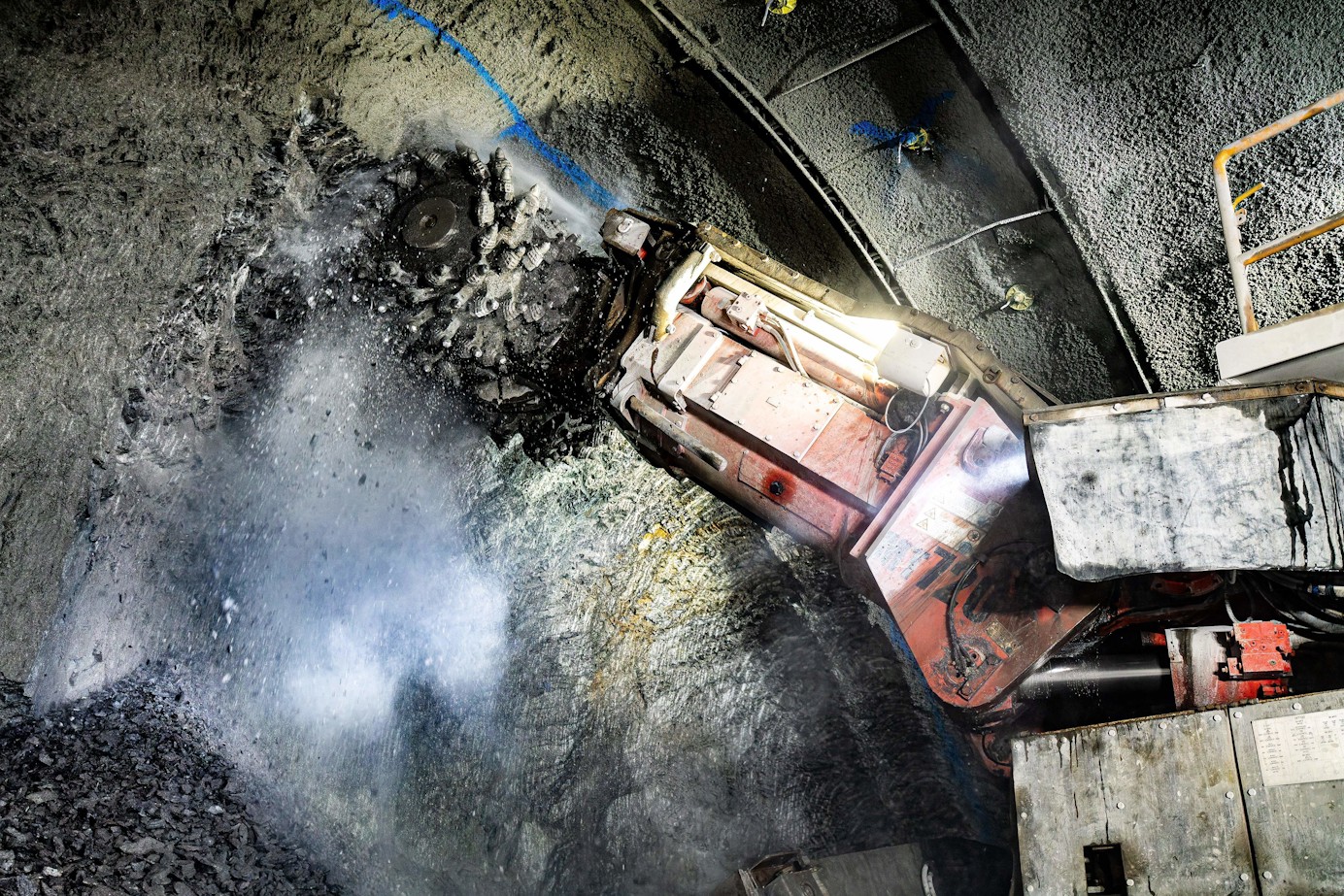
Operators received hands-on simulation and theoretical training in Austria, which helped accelerate their familiarity with the system. According to Hong-joo, the machine is not only user-friendly, but also safe and comfortable: "We set up our design program, communicate, and run an automated program, which proved extremely precise. It was great that errors in the equipment were clearly shown on the monitor."
The benefits go beyond operator satisfaction. According to site manager Jun-Won Eom: "Even though we are using a high number of picks and low cutting speeds due to the hard rock, the MT720 has overcome all the tough conditions."
“One month ago, we excavated one meter in just one hour. I think this machine is number one in the world.”
A true partnership in progress
The collaboration between SK Ecoplant and Sandvik goes beyond a standard supplier-client relationship. Sandvik has been an active partner from the design stage to operator training and on-site service.
"The cooperation started early. From design to implementation, Sandvik supported us with knowledge and on-the-ground help." Jun-Won Eom
Sandvik engineers frequently visit the site to assist with maintenance, address issues, and ensure maximum uptime. "Whenever there were any questions about the equipment, just call Sandvik, and they’ll resolve everything quickly. That was very helpful." Operator Jin-kyo Seo
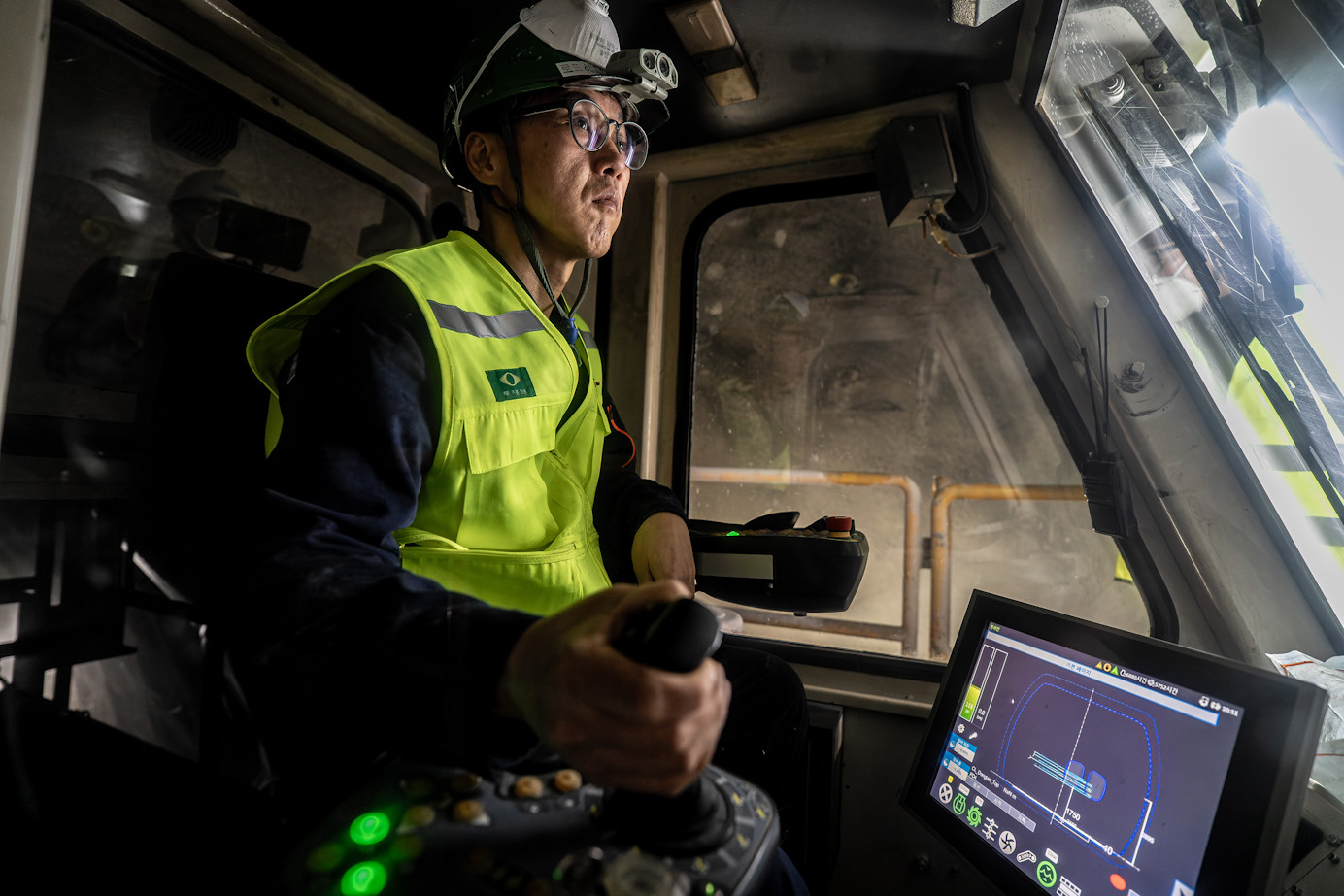
"We anticipated many neighborhood complaints due to noise. But in the section using the Sandvik MT720, there were none. Not a single complaint. That allowed us to keep working without interruption." Structural Engineer Logan Ryu.
“The machine helps us work faster and with fewer delays. It’s one of the main reasons we were selected as the successful bidder for the second phase of this project.”
Looking ahead: A model for future urban tunneling
With 600 meters already excavated and 700 remaining, the project is progressing smoothly. Thanks to its low noise and vibration, Sandvik MT720 is allowing SK Ecoplant to work day and night, meeting schedule expectations while maintaining safety and environmental standards.
"I believe the mechanical excavation method will be used more and more in Korea, especially in urban areas," said Jun-Won Eom. "Sandvik has proven they’re not just a supplier they’re a reliable partner with the best equipment in the world."
This project isn’t just about meeting deadlines. It’s about setting a new standard for how sustainable, efficient, and collaborative underground construction can be.
"If someone asked me whether to recommend this equipment, I would say without hesitation: It’s excellent." operator Kim Hong-joo
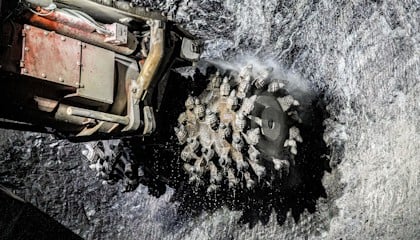
Key features of the Sandvik MT720/MT721:
- Cut service costs and increase productivity - robust machine design and optimized transverse cutter heads use ICUTROC® cutting technology for cost-effective rock cutting in different rock conditions, increasing machine availability while decreasing machine service costs.
- Optimize machine application - Various digitalization options increase machine application versatility, including teleremote operation, fleet data and telemetry data monitoring via Racoon and SmartMate software solutions.
- Semi-automated operation for simpler onboarding - CUTRONIC® enables semi-automated cutting and assists roadheader operation for rookies in mechanical rock excavation, optimizing customer value.
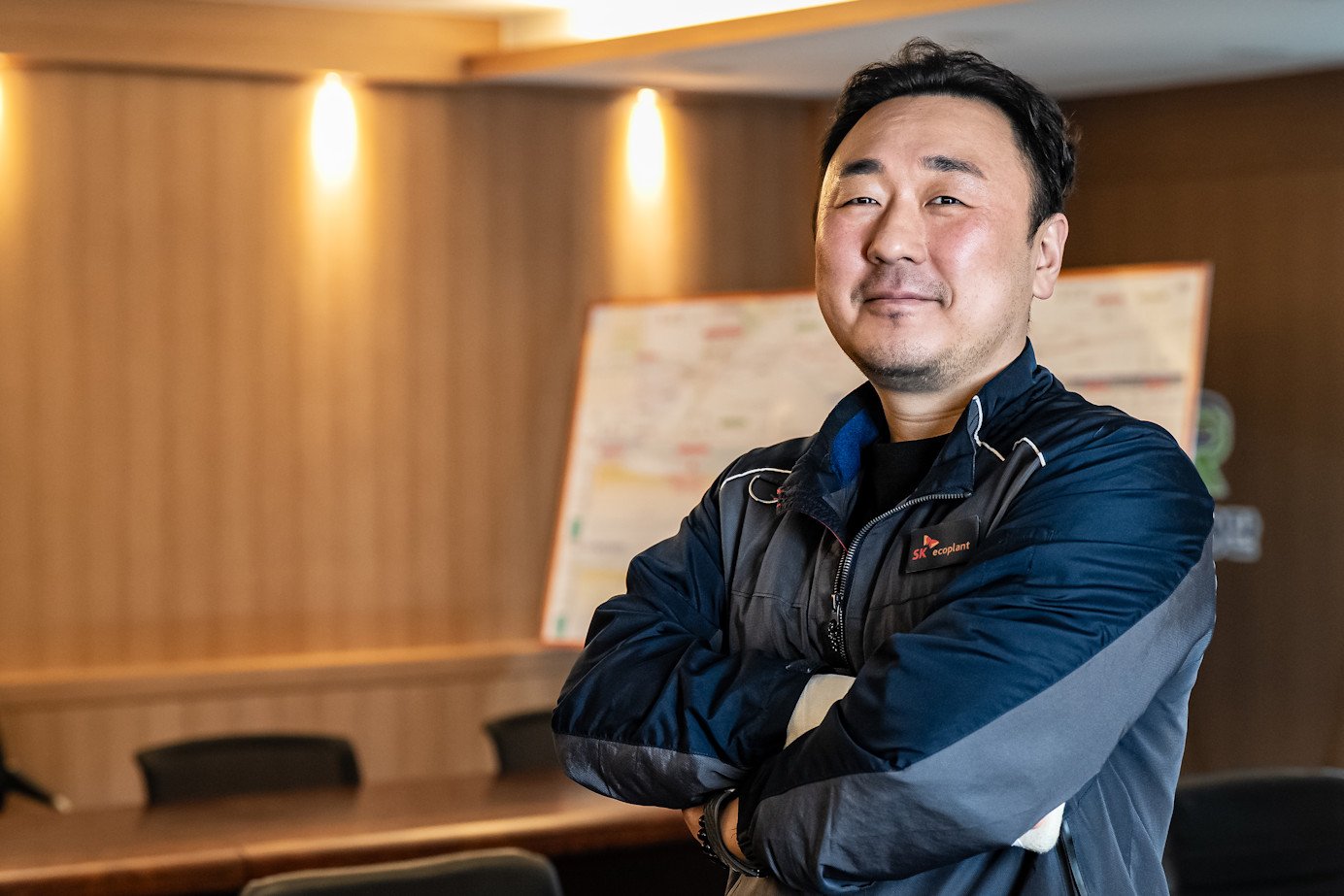